Nel precedente articolo vi ho parlato del motore e di quanto sia importante ottimizzarlo per avvicinarsi il più possibile alla condizione ideale prevista dal ciclo aria-combustibile. Vi ho poi raccontato di come gli ingegneri cerchino di ridurre le zone rosse (perdite di energia) e di far sì che l’area in verde nel grafico sia la più piccola possibile così da ridurre il lavoro di pompaggio.
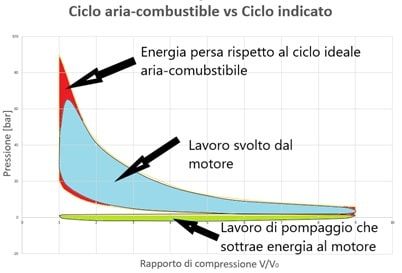
Ma come si attua nella pratica tutto ciò? Come si può far sì che l’area azzurra si espanda a discapito della parte rossa? Come si fa ad assottigliare ancora di più l’area in verde?
Il segreto sta nel tempismo con cui avviene l’apertura e la chiusura delle valvole di aspirazione e di scarico.
A differenza del ciclo ideale, in un motore, il movimento reale delle valvole non è istantaneo ed è perciò cruciale che il tutto sia in perfetta sincronia.
Per rappresentare la corretta sequenza, ci si avvale del diagramma circolare di distribuzione che descrive gli anticipi e i ritardi di ciascuna valvola al variare dell’angolo di manovella. Guardiamo ora il diagramma e iniziamo ad analizzare le varie fasi.
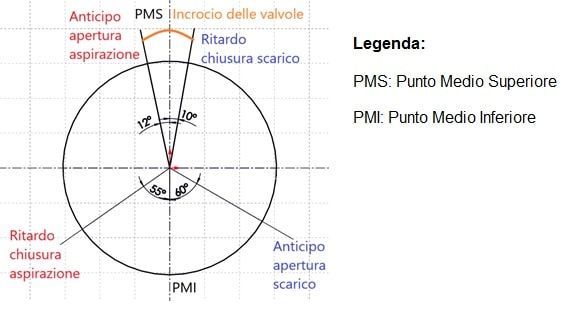
L’anticipo di circa 12° gradi dell’apertura all’aspirazione fa sì che la valvola sia completamente aperta quando il pistone raggiunge il punto morto superiore. In questo modo l’aria incontra meno “ostruzione”, il cilindro si riempie in maniera migliore e il lavoro di pompaggio si riduce significativamente.
La chiusura della valvola di aspirazione in ritardo di circa 55° rispetto al punto morto inferiore, consente di sfruttare al massimo l’inerzia della colonna di aria entrante (onda di sovrapressione). Così si migliora il riempimento del cilindro e si aumenta la densità dell’aria all’interno dello stesso.
Per quanto riguarda lo scarico, invece, le cose sono diverse.
L’apertura della valvola viene anticipata di circa 60° rispetto al PMI per ridurre la contro pressione che si oppone al moto del pistone durante la corsa di ritorno. In questo modo si perde un po’ di lavoro utile, ma in compenso si riduce significativamente il lavoro di pompaggio richiesto per espellere i gas all’interno del cilindro. La chiusura dello scarico avviene con un ritardo di circa 10° per sfruttare l’inerzia della colonna di fluido nel condotto di scarico.
Si ha così un ottimo lavaggio e un buon riempimento del cilindro. In questa delicata sequenza si ha una fase critica in cui sia la valvola di scarico che quella di aspirazione sono aperte contemporaneamente. Questa è una situazione particolarmente problematica ai bassi carichi. Questo perché la pressione all’interno del cilindro è maggiore di quella presente nel collettore di aspirazione, cosicché una frazione dei gas di scarico entra nel condotto di aspirazione diluendo in parte la carica fresca entrante. Tutto ciò causa una perdita di efficienza e prestazione di cui l’ingegnere deve tener conto.
Fondamentale è poi la tempistica entro cui avviene la combustione. In genere la scintilla scocca con un anticipo di 7-8° rispetto al PMS. In questo modo si può sfruttare parte della fase di compressione per innalzare la pressione massima P3 del ciclo.
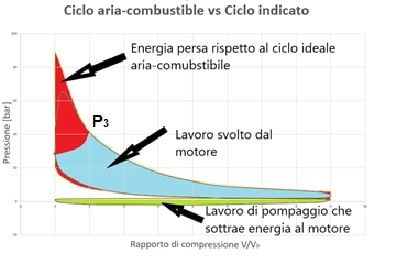
Come si vede nel grafico, se la combustione avvenisse esattamente al PMS si perderebbe moltissimo lavoro utile.
Abbiamo quindi capito che per migliorare le prestazioni di un motore bisogna estrarre il massimo lavoro utile. Bisogna cioè rendere l’area azzurra il più grande possibile. A questo punto vi chiederete. “Ma se invece che muoversi all’interno dell’area delimitata dal ciclo ideale, allargassimo i limiti imposti dallo stesso ciclo aria-combustibile?”.
Questo è possibile e significa aumentare la potenza del motore. Nel prossimo articolo si parlerà proprio di questo: vedremo come stimare la potenza di un motore e su quali parametri agire per migliorare le prestazioni.
I commenti sono chiusi.